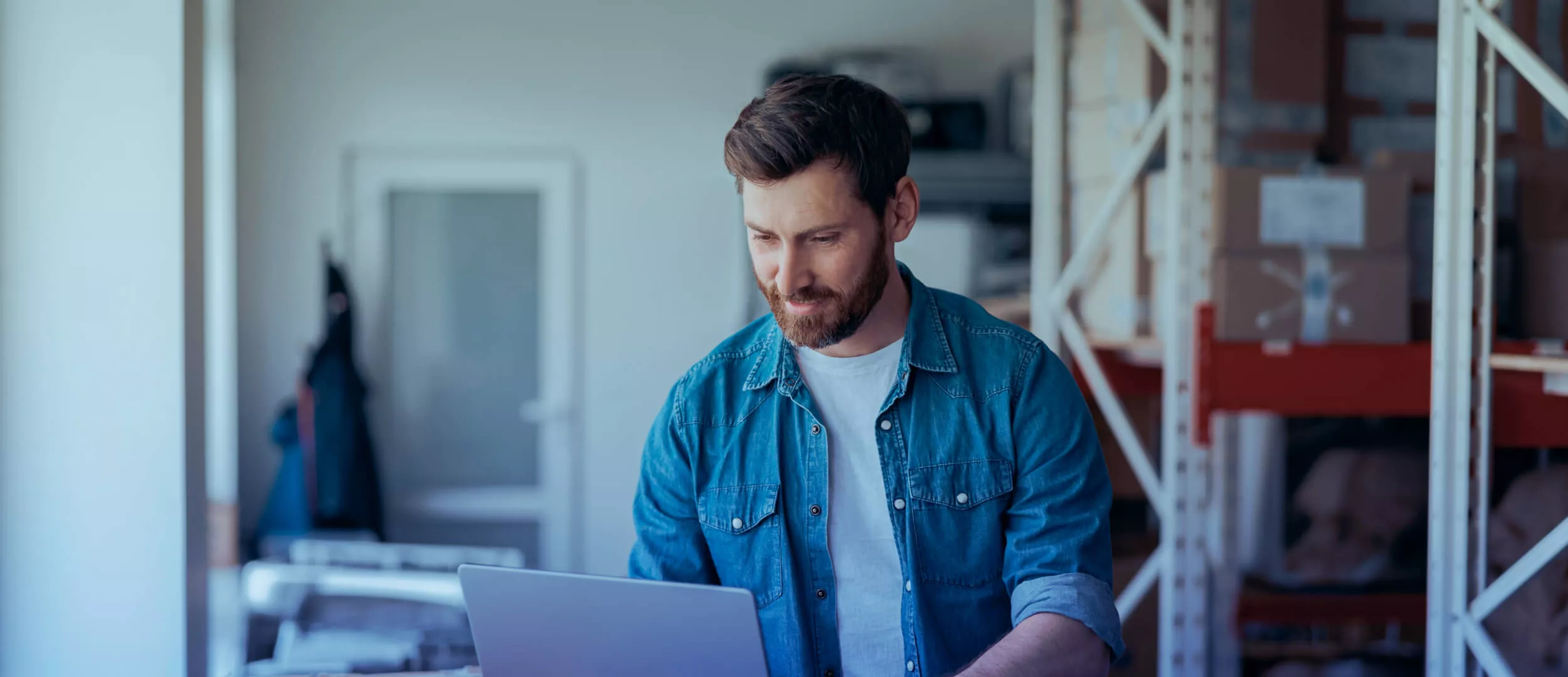
Creating an inventory system helps companies improve their management. It controls levels, reduces costs, and prevents stock-outs and overstocking. If you're a tech-savvy retailer who prefers not to use third-party software, you can create a simple system to help with your supply chain operations.
In this blog post, we'll show how to develop inventory management software.
What is an Inventory Management System?
An inventory management system tracks goods throughout the supply chain, from purchasing to production to sales. It helps you manage items efficiently and maintain healthy margins.
If you have a lot of products, an effective system is essential. Companies dealing with physical goods need a way to manage inventory.
For some, an Excel or Google Sheets spreadsheet is enough. However, many prefer dedicated software to improve efficiency and reduce costs.
The best system for your business depends on its size, complexity, and needs.
Types of Inventory Management Systems
Creating a custom system offers many options to meet all your business needs. It's helpful to look at the two main types of systems to understand their uses.
General-purpose systems
1. Custom Inventory Management Software
- Helps create unique solutions tailored to a business's specific needs.
- Functions: control, item management, order management, supplier management, analytics, and database management.
Want a web app that does more?
Let's build a solution that's smart, sleek, and powerful.
Alina
Client Manager
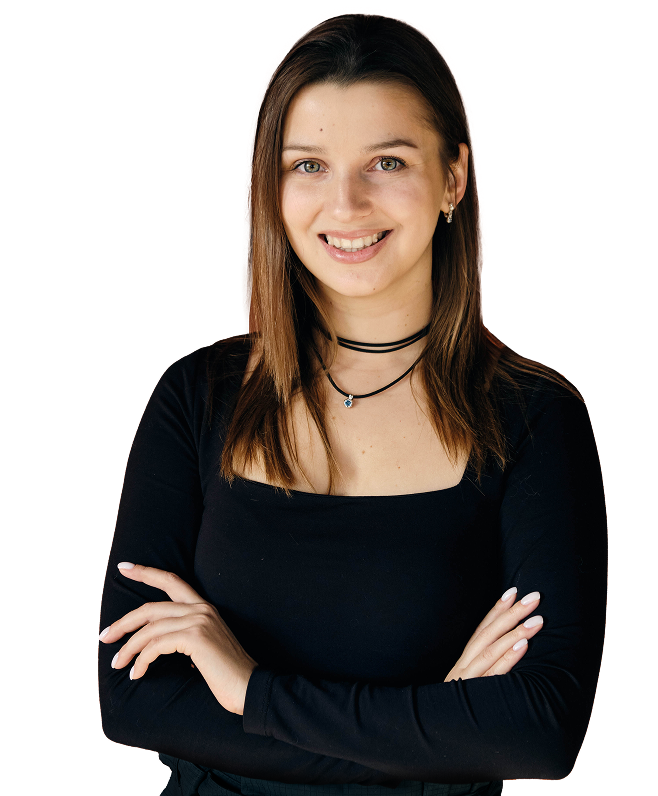
2. Inventory Database Software
- Centralized repository for all data.
- Types: spreadsheets (Google Sheets, Excel), database apps (LibreOffice Base, Microsoft Access), and custom database software.
- Key Features: data storage, navigation, database management, control, and advanced analytics.
3. Inventory Automation System
- Automates valuation, auditing, levels, location, ordering, and selling.
- Ideal for large enterprises with complex inventories.
- Plan Elements: planning, SKU management, ordering, costing, reservation, control, custom orders, optimization, reverse logistics, and analysis.
4. Stock Control Software
- Monitors stock costs, levels, and value.
- Quickly locates items and sends alerts for replenishment.
- Features: database management, control, item management, tracking, order management, analytics, and reporting.
5. Inventory Counting Software
- Counts stock faster and more accurately using barcode/QR scanners, RFID devices, and computer vision.
- Use Cases: storage, points of sale, and manufacturing.
- Key Features: counting automation, control, replenishment, reconciliation, validation, and reporting.
6. Optimization
- Balances stock levels to avoid overstocking or shortages.
- Key Features: demand analysis, safety stock computation, data analysis, optimization model management, cost analysis, and prescriptive analytics.
Industry-specific inventory solutions
When creating a simple system, it helps to look at examples from different industries and their specific needs:
1. Retail Solution:
- Used by retailers to manage multiple channels and locations (warehouses, stores, online shops).
- Features: point-of-sale integration, barcode scanning, customer loyalty programs, omnichannel sales tracking, and artificial intelligence.
2. Manufacturing Inventory Systems:
- Used by manufacturers to plan and control production and distribution.
- Features: kitting and assembly, quality control, work order management, bill of materials.
3. Healthcare Inventory Solutions:
- Helps healthcare providers manage drugs, equipment, and supplies.
- Features: expiration date tracking, regulatory compliance, lot number tracking, and serial number tracking.
Each system is designed with features tailored to the specific needs of its industry.
Must-have inventory management features
Knowing how to create a simple inventory management system starts with essential features to ensure smooth business operations. These features include:
- Barcode Scanner. Reads product barcodes to quickly input details like product information and price. It speeds up tasks like receiving, packing, picking, and shipping while reducing errors.
- Reporting. Generates reports and charts based on inventory data, helping monitor and evaluate stock performance, turnover, value, and sales trends.
- Forecasting. Helps predict and plan for future needs, ensuring you have the right stock at the right time.
- Accounting. Tracks financial data such as prices, gross profit, and income statements. It helps with budget compliance and valuation methods like FIFO, LIFO, and average cost.
- Point-of-Sale Integration. This connects your solution with your POS, updating data in real-time whenever sales are made in physical stores.
- Inventory Alerts. Sends automatic alerts for low or high stock levels, product expiration, pending orders, and overdue shipments. It helps you stay on top of status.
- Automatic Reordering. This ensures timely stock replenishment without human intervention, maintaining optimal stock levels.
- Logistics. Helps manage the distribution and delivery of inventory, optimizing the flow of goods across different channels and locations.
Pros and cons of creating a custom inventory system
Inventory management software development can greatly benefit your business, especially when working with a specialized logistics software development company.
Pros
- Integration. It connects easily with other software you use, like eСommerce platforms, accounting software, or point-of-sale systems. This makes data flow smoothly across your business.
- Flexibility and Scalability. A custom solution can change as your business needs change. It can also grow with your business, handling more items and complex processes.
- Enhanced Efficiency. Customization reduces manual work and errors, saving time and money, and making your business more efficient.
- Better Data Management. A tailored system helps you manage and analyze your inventory data, providing insights for better decisions.
- Improved Customer Service. It means faster response times and accurate order fulfillment, leading to satisfied customers.
Cons
- The cost. Creating a custom inventory system can come with significant expenses. Including the cost of hiring front-end and backend development experts to build and maintain it. Ongoing updates and support further add to the financial commitment.
Additional resources. Implementing such a system may require thorough training for your staff. They need to effectively navigate its unique functions and workflows.
Technical Challenges. Without experienced engineers, custom software can have technical problems. Compatibility problems or design errors can affect the system's reliability.
How to Create an Inventory Management System in 8 Steps
Finally, let's talk about how to create inventory management software. What are the best practices? From our experience, here are the key steps.
Develop an architecture and design of the system
Knowing how to build a simple inventory management software, starts with figuring out what features you need. It can be tracking items, managing orders, and generating reports. Think about how the system can grow and connect with other tools in the future.
Choose a three-part structure for the system. One part for the user interface (UI), another for the business logic, and a third for the database. For bigger systems, you might break it into smaller, connected services.
Design the database with tables for products, categories, suppliers, orders, and users. Make sure the tables are connected properly, like linking products to their categories.
Plan the user interface with simple and clear screens for dashboards, inventory lists, and order forms. Make sure it's easy to navigate.
Decide on the rules for how the system will manage inventory levels, process orders, and create reports. Ensure data is accurate, like not allowing negative stock levels.
Create a tech stack
Creating a tech stack means choosing the technologies and tools to build and run the solution. This includes:
- Programming languages (like Python, C#, Java, PHP, Swift)
- Databases
- Platforms
- Frameworks
- Libraries
Your tech stack depends on your system’s needs and goals, budget, and timeline. It's also important to consider how well your chosen technologies will work with other systems or services you might use or connect with.
Setting Up User Interface (UI)
The next step is to set up a user interface (UI) based on the relationships created in the database.
Your UI needs to be simple and intuitive. This UI aims to help users easily navigate the core functionalities. For example, tracking, managing orders, and supporting users who can log in from various locations.
Refrain from complicating the UI. A simple interface can affect user experience, leading to clarity and complaints. Keep it clean, straightforward, and user-friendly to ensure users can perform their tasks.
Integrate the software with other systems
Next, integrate your software with other systems. It can be sales, accounting, logistics, and purchasing. This ensures all your data stays up-to-date and consistent across these services.
For example, when a sale is made, the sales system updates your inventory levels automatically. Connecting with accounting software helps keep financial records accurate. Linking with logistics improves tracking and delivery. Integrating with purchasing automates reordering when stock is low, a crucial benefit of inventory management application development.
Migrate inventory data
Migrating data for inventory management system involves transferring your existing information to new software. Here’s how:
First, clean your data to ensure accuracy by removing duplicates and outdated entries.
Next, export your data into a CSV or Excel file from your current system. Prepare the new software by ensuring it's ready to receive the data and that fields match. Import the file into the new system using its tools, ensuring data is correctly mapped. Verify the transfer by checking for errors or missing entries, using reports or manual checks.
Purchase Order Management
Purchase Order Management in custom inventory management solution development involves creating, tracking, and managing. Key features include:
- Generating purchase orders based on inventory levels.
- Sending orders to suppliers.
- Tracking order statuses.
- Receiving and updating inventory upon delivery.
- Integrating with accounting for smooth financial operations.
- Effective PO management streamlines procurement, reduces errors, and optimizes inventory levels.
Conduct user training
To ensure your custom inventory management software is used effectively, invest time and resources in training your users. Provide clear and comprehensive training materials and sessions on how to access and navigate the system, perform different tasks, troubleshoot issues, and more. You can use manuals, videos, workshops, and webinars to deliver this training. This helps users maximize their understanding and use of the software, leading to better operational efficiency.
Create a support service
Providing ongoing support and maintenance for your inventory management system is crucial. This ensures smooth operation and quick resolution of any issues. Regular maintenance includes updating the software, fixing bugs, and addressing user concerns. By maintaining your system effectively, you can maximize its efficiency.
Costs of Inventory Management System Development
Several factors significantly influence the cost of inventory management development.
1. Type of System. Whether it's a software-only solution or involves hardware components.
2. Features. The number and complexity of features like tracking, reporting, etc.
3. User Roles. The complexity of user roles and permission settings.
4. UX/UI Design. The uniqueness and complexity of the user interface and experience.
5. Data Migration. If there's a need to migrate data from existing systems.
6. Integrations. The scope and complexity of integrating with other systems.
7. Performance Requirements. Including availability, security, scalability, and performance needs.
8. Development Model. The sourcing model and team composition chosen for development.
Developing an inventory management system usually costs between $80,000 and $350,000. The cost depends on complexity, features, integration with other systems, and customization. Spending more often results in a better, more customized solution.
Why Build Your Inventory Management Software with Stfalcon
Having control over your system is crucial for a successful business. However, managing it can be overwhelming and time-consuming.
Inventory management software development company Stfalcon offers several advantages. We have expertise in developing custom software solutions, including robust management systems. Stfalcon can tailor the software to fit your specific business needs. We emphasize quality assurance through rigorous testing, delivering reliable and high-performing software.
Stfalcon provides ongoing support and maintenance to ensure your software runs smoothly over time. We stay updated with the latest technologies and trends. Also, incorporate innovative features into your software solution.
Stfalcon received the Clutch 1000 Award in 2023 for its customer-focused approach, professional expertise, and successful track record in creating valuable product offerings. Also, TÜV NORD CERT GmbH has officially certified that Stfalcon Web and Mobile Development Company operates a management system that meets ISO 9001:2015 requirements.
Choosing Stfalcon ensures you get a tailored, reliable, and cutting-edge inventory management software solution for your business needs.
Conclusion
We have explored how to create management software. We've delved into developing inventory management application essential components, features, and best practices. This process is accessible to any business and offers numerous benefits, particularly to those whose operations greatly benefit from streamlined control. By implementing custom inventory management software, businesses can enhance efficiency, reduce errors. Also, improve decision-making with real-time data, and ultimately optimize their overall management processes. If you are interested in creating a tailored solution, contact us today!
Here are answers to common questions about how to create an inventory system.
FAQs about Building Inventory Management Software
How long does it take to develop inventory management software?
The timeline for completing the project depends on its size and complexity. Building a management app usually takes 400 hours. However, it can take as little as 267 hours or as much as 667 hours. The time needed mainly depends on how complex your app is.
How much does it cost to develop an inventory management system?
Developing this kind of system ranges from $80,000 for a basic one to $350,000 for a more complex one.
Can inventory management software be customized?
Custom software is a personalized solution crafted to match the distinct needs and workflows of a business. It enables precise control and optimization of inventory processes.